Timing is Everything
, discusses the risks of adopting welded aluminium internal floating roofs prematurely. Read more below or
The Apple Newton, internet grocery delivery services, video laser discs, and the General Motors EV1 were all products that were ahead of their time, and all were destined to fall short of their initial promise. Most often these failures were the result of imperfect technology, a lack of robust infrastructure, and high costs which prevented a successful return on investment. And yet, all these inventions returned, in time, as the iPhone, Instacart (among others), DVDs, and Tesla. Once all the necessary elements had been worked out, each became a successful product.
The storage tank industry is not immune to such excursions into new and promising yet under-developed and unproven technologies. One recent example is the introduction of welded full-contact aluminium internal floating roofs (AIFRs). A noble idea, but one that, like the earlier examples, is ahead of its time.
The industry has historically been very slow to adopt new technologies, regardless of the promise of improved efficiencies, improved safety, and decreased environmental risk or emissions – and rightfully so. The risks of taking on new, unproven technology are simply too high. Consequences can include tank cleaning to remove a malfunctioning product, reputational damage from an accidental product release, or worse, a safety incident where someone is hurt or killed. These costs make the industry understandably wary of replacing tried and trusted solutions, even if imperfect, with newer products or methods that lack a proven track record and operating history.
And yet, every once in a while, a product or work method comes along that holds so much promise, and represents such a great leap forward, that it is worth the risk.
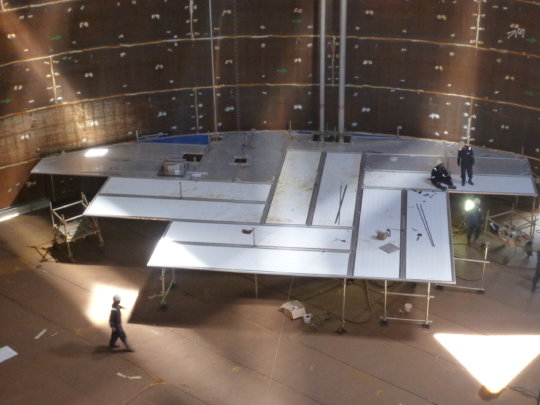
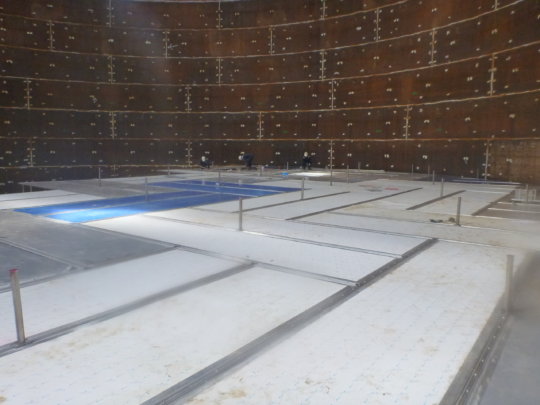
A closer look at the AIFR
AIFRs were once considered unorthodox, given their lightweight design and relatively limited lifespan, at least compared to traditional carbon steel roof designs. Environmental considerations such as the desire to eliminate or minimise vapour spaces as would be found in cone roof tanks without floating roofs, coupled with the economics of reducing product heel, led to the introduction and lengthy adoption of this new technology. Many expensive lessons were learned along the way, as can be relayed by terminal operators everywhere. Nonetheless, over time, as lessons were learned and technologies and designs improved (pushed along by competition and customer demands), AIFRs earned their place in the industry.
AIFRs, however, also have a shortcoming in relation to emissions. They are generally constructed from component pieces, bolted and sealed together with gaskets and various sealing mechanisms. These designs result in a seam which, despite advanced designs and gasket material, is viewed by environmental and industry regulators as a point of emission. Conversely, a carbon steel roof, with all of its components welded together,does not have these kind of seams, and therefore no such emission points, except for the numerous leg penetrations that must inherently exist to support such a large structure.
This has led people to question whether it would be possible to weld the components of an aluminium roof together, in the same way as with a carbon steel roof, and eliminate the seams in order to remove the point of emissions.
Just as people pondered the possibility of a handheld computer, an internet service to deliver groceries, a video laser disc or a car that runs on electricity: all worthy and good ideas, and each lacking technology somewhere along their value chain, making them ahead of their time.
The welding of aluminium, while very common, is more difficult than the welding of steel for the following reasons:
- Aluminium does not change colour when it melts, making the weld puddle difficult to distinguish.
- Aluminium material quickly forms an oxide layer that melts at a higher temperature than the material itself. Therefore, the aluminium must be thoroughly cleaned just prior to welding (preferably on the same day) in order to set proper welding parameters. This is a challenge when welding is conducted outside of the clean and controllable confines of a shop or inside a tank, for example.
- Aluminium is also highly susceptible to porosity from the slightest amount of contamination, making it very difficult to avoid. After an AIFR has been in service, the product becomes embedded in these pores, making welding almost impossible.
The inside of a storage tank, whether newly constructed or under maintenance, is a relatively dirty space with many potential contaminants. The welding of sheet or panels in the field can be inherently more difficult than the same process conducted in a controlled factory setting, setting up the potential for porous welds and cracks which have the potential to leak.
One of the historic benefits of AIFRs has been that in the event of damage, component parts can be easily switched out, given their modular nature. Welding these components into one large piece effectively eliminates that benefit. Moreover, if product has seeped into a roof through a cracked or damaged weld, it can create a potentially flammable environment during any hot work, such as cutting apart the roof, that may not be immediately evident.
Things to consider
With this in mind, if considering a welded AIFR, tank owners and operators will need to ask themselves whether the benefits of a fully welded AIFR outweigh the potential costs and risks.
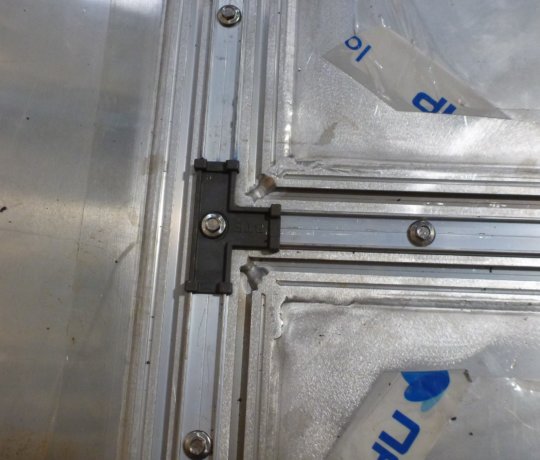
More broadly, it is important to consider what ‘early adopters’ can do to safeguard against the potential downside of any new-to-the-market product. Certainly, a warranty beyond industry standard terms should be an option. If a product vendor has considered all aspects and completed thorough research, development and testing of their new product, they should have the confidence to stand behind it while it goes through a proving stage.
Secondly, tank owners and operators should ask for multiple references from those who have had the product installed for the longest period of time and, therefore, have some operational experience with the product.
Finally, when imagining the downside risks of any product that is fairly new to the market, tank owners and operators should ask themselves:
- What potentially could go wrong?
- What are the difficulties in manufacturing and installation?
- What is the total cost of a product failure, and is it easily remedied?
Product failures in the tank and terminal industry have the potential to be very costly. Therefore, new products, whether an AIFR, a new valve design, or cutting-edge emissions control devices, should always be viewed with a fair amount of caution and forethought.
Technologies and processes very often advance over time and, ultimately, many of the products that were first to market (and commercially or technologically unsuccessful) become ubiquitous, indispensable, and the new industry standard. They just need the underpinnings of infrastructure and process, much of which is developed through the learnings of earlier failures.
New technologies are great, but timing is everything. Caution should be taken in adopting them too early if the downside risks and costs outweigh the benefits.